Just got back results from arbsession, email of the graph came first, had 40% reduction in break strength. I pay the extra to have broken bits sent back to me. Good thing this time, the splice survived, but rope broke at the drum they wrap it around, would have thought it was the splice otherwise. Wrapping drums are how a lot of rope manufactures determine the break strength of their ropes.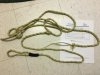
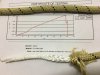
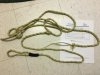
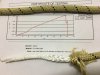